
Serving Grand Rapids
and nearby areas
"Happy Window Cleaning provides the best views"
TRAINING - SAFETY CULTURE
There isn’t anything more important than profit, customer experience, and anything else that we are involved with during doing business. It is up to each individual to keep safety foremost in his/her mind. Every employee must know that if they feel something is not safe then they must not do it! This priority must be expressed in writing and become a part of the company orientation process. Anything less would reflect negligence of duty to your employees. Everyone must keep the workplace safe for customers, passersby, and employees alike. Employees from the least to the greatest must be informed that It is their responsibility to report all unsafe conditions to their immediate superior.
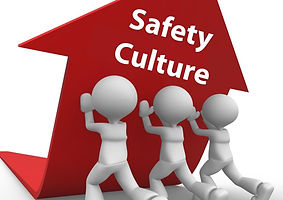
A Hazard Communication Program is mandatory for all cleaning companies. Chemicals are a part of our world and we encounter cleaning supplies, disinfectants, fuels, pressurized containers, paint, and sealers on the job site. All of these items present both acute and chronic health hazards. The acute effects are those which are immediate or occur within the short term, the symptoms appear just after exposure to the agent. Typically, these occur due to accidents on the job site that involve high concentration, corrosives, acids, irritants, allergic reactions, rashes, burns, respiratory irritation, respiratory failure, eye injury, and poisoning.
Other health hazards occur over long periods and are called chronic illnesses. These are the long-term effects of being exposed to hazardous agents. The symptoms appear long after exposure. These types of illnesses are caused by even low concentrations of toxic agents such as neurotoxins and carcinogens. Some of these include cancer, lung or liver damage asthma, COPD, and allergies.
Your safety orientation must include a segment explaining to employees how chemicals enter the body. These include inhalation, meaning they are breathed through the mouth or nose. Absorption occurs when chemicals either touch the skin or are injected into the body. Ingestion means the chemical was swallowed, and ocular entry, through the eyes.
Federal and state law requires that all hazardous agents be properly labeled. It is the responsibility of the staff to check labels before use for the identity of the chemical, the name, and address of the manufacturer, and appropriate hazard warnings. Employees should regard unlabeled containers as dangerous, therefore, employees must never remove labels.
Material Safety Data Sheets are prominently displayed with the words “EMPLOYEE’s RIGHT TO KNOW” available for employees to examine and with such knowledge comes the responsibility to ensure that all recommended precautions are properly taken. The Material Safety Data Sheet contains detailed information that was prepared by the manufacturer or importer. There should be a sheet available for every hazardous chemical or substance. The Material Safety Data Sheet (MSDS) contains information that enables you to prepare for the safe day-to-day use of the agent as well as arming you with the information you will need to respond to emergencies.
Specific information provided on an MSDS is the chemical name, company information, hazardous ingredients, physical characteristics, fire, and explosive data, health hazard data, reactivity data, and special precautions including safe handling instructions, personal protection equipment (PPE) which must be worn when handling the agent and what to do in case of spills or leaks.
The Company Safety Orientation must include a segment on “General Work Practices”. Employees must be instructed that they are permitted to use hazardous chemicals only as directed. Before using hazardous chemicals, it is the employee’s responsibility to inspect equipment for damage and to ensure adequate ventilation. If there is any doubt or question as to how to proceed, stop what you are doing, and ask the safety supervisor for help. When using the hazardous chemical do not smoke, eat drink, text, talk on your cellphone, or apply cosmetics. Never smell inhale or taste a hazardous chemical. Keep hazardous chemicals off of hands, face, clothing, and shoes. After use, be sure to wash hands and face thoroughly with soap and water.
Employees must be instructed about and acknowledge that they have been instructed on the known safe handling procedures per the label and MSDS, specific information on flammability, incompatibility, and stability. Employees should be asked to sign a form that states the particular item that he or she has been instructed in the proper use of the specific hazardous chemical.
There must also be a Standard Operating Procedure that everyone is familiar with in case of exposure occurs. If exposure is due to inhalation move yourself or your coworker to fresh air. For the eyes flush with water for fifteen minutes. For the skin exposures, wash with soap and water. If a hazardous chemical was swallowed seek immediate medical help. Report the incident to your superior. If a co-worker is exposed try to determine the type of hazardous chemical. Refer to labels and MSDS for specific instructions. Report the incident to your superior.
In summary, chemicals present both physical and health hazards and employees have the right to know about all possible known hazards at the workplace. It is most important that employees read and become familiar with the labels and MSDS for each hazardous substance and that they learn to follow PPE and special handling recommendations. Finally, there must be an Emergency Response Plan in case there is exposure to a hazardous substance. This must include the provisions to notify the supervisor and to know immediate first aid response if one comes into contact with a hazardous chemical.
The requirements for personal protection equipment are found on labels and MSDS. A safe workplace has the following Personal Protection Equipment (PPE) handy in case of an emergency:
• Gloves (These are many types with varying effectiveness. The right gloves (thickness, material length, etc.) must be worn for a particular task.
• Respirators & Dust masks. There are different types and the wrong type for the task offers no protection at all.
• Head protection
• Tongs
• Aprons or full bodysuits. These require a thorough inspection for rips and punctures, as well as a decontamination procedure.
• Safety glasses. Protect your Eyes. Safety glasses guard against forceful impacts and heat exposure. They are made to withstand the impact of a quarter-inch metal ball traveling at a hundred and fifty feet per second. Most safety glasses are equipped with side shields. Safety glasses must fit the wearer correctly. Goggles provide a secure shield around the eyes to guard against flying debris. Goggles should be worn over contact lenses if in areas with dust or chemicals. Like safety glasses, goggles must fit the wearer correctly. There are special lenses made for goggles to protect against bright light.
Personal Protection Equipment requires maintenance. Protective eyewear, for example, will not withstand repeated impact or abuse. If your PPE is worn or seems to have surpassed its useful life, inform your superior. Replace them when they are worn, broken, or if you cannot see out of them for any reason. Replace knotted, twisted, worn, or stretched-out goggle straps. Clean equipment after every use.
Remember that the equipment cannot protect you if you fail to use it. It is everyone’s responsibility to be aware of their environment. The eyes can be damaged from forceful impacts, such as from moving machinery especially that which is moving at high RPMs (revolutions per minute). Small particles, chemicals, liquid metal, heat lasers, and radiation all present unique hazards which can damage the eyes.
Eye Injuries from Chemical Burns. To treat eye injuries from chemical burns, use a portable eyewash station, continue rinsing eyes for fifteen minutes or until help arrives.
Back Injuries. Eighty to ninety percent of people will have back injuries to some degree in their lifetimes. One out of every five workplace injuries is a back injury. Seventy-five percent of all back injuries are preventable because they occur while lifting. Common causes of back injuries include lifting too much weight. Improperly lifting using poor technique, i.e., bending over at the waist, twisting with the load, reaching for elevated loads, and carrying or lifting awkwardly shaped or cantilevered objects. Another type of injury occurs when we are standing, sitting, or working in one position for too long without adjusting to avoid injury.
Proper Lifting Procedures. Think before you lift. Test the load before lifting it. Place feet shoulder-width apart close to the object. Bend the knees and get a secure grip on the object. Lift with the legs, keeping the back straight. Lift evenly and slowly, do not jerk the load. Keep the load as close to the body as possible. If you must change the direction that you are facing while carrying a load do not twist the torso, but rather turn the feet in the direction of intended travel. Allow the body to follow the feet. When moving with the load keep it close to the body. Watch for slip and fall hazards. To let the load down, follow the steps in reverse.
Key takeaways from this segment of the safety orientation are: Use proper lifting techniques. Know how to avoid dangerous motions. Don’t overdo it, ask for help. And take care of your back it is the only one you’ve got!
Safety Meetings/Morning Huddle:

It does not matter if you are having toolbox safety meetings that are only five minutes daily or hour-long safety meetings once per month. Safety meetings are a powerful activity for reducing accidents and promoting all aspects of safety.
Safety meetings show management values safety.
Employees realize that management only invests time and money in what is important. Creating a work environment where safety is valued requires an investment.
At work and home, we find time for those activities we value most. If family and friends are important to you, you make time for those relationships. If fitness is important, you make time to exercise. We recognize time is our most precious commodity, so we reserve it for what matters most to us.
If a company talks about safety but spends little or no time on structured safety efforts, then employees may feel safety is not important. Safety will slide to the back of their mind, and their efforts will be focused on what they perceive management holds as important.
Always review safety procedures with new hires to make sure that they understand the dangers and precautions necessary to work safely in this environment.
See to it that your Happy Window Cleaning® franchise personnel are familiar with all equipment necessary to operate this business model and refer to HQ with any questions or concerns about particular policies.
The benefits safety meetings can provide include:
• Engage and enlist the help of employees
• Promote the importance of safety by showing a company’s willingness to invest time
• Allow employees to contribute. Remember, they are the ones that know the unsafe conditions and behaviors
• Provide the opportunity to teach safety topics in a short effective manner that employees will remember, as opposed to long training sessions that can be boring
• Provide a level of awareness, teamwork, and community
• Meetings will not only speed up the establishment of a safety-first culture, but they are also crucial to maintaining it. They provide consistency to the company’s safety message
Ladder Safety:

Ladders are tools. Many of the basic safety rules that apply to most tools also apply to the safe use of a ladder:
• If you feel tired or dizzy or are prone to losing your balance, stay off the ladder.
• Do not use ladders in high winds or storms.
• Wear clean slip-resistant shoes. Shoes with leather soles are not appropriate for ladder use since they are not considered sufficiently slip-resistant.
• Before using a ladder, inspect it to confirm it is in good working condition. Ladders with loose or missing parts must be rejected. Rickety ladders that sway or lean to the side must be rejected.
• The ladder you select must be the right size for the job. The Duty Rating of the ladder must be greater than the total weight of the climber, tools, supplies, and other objects placed upon the ladder. The length of the ladder must be sufficient so that the climber does not have to stand on the top rung or step.
• When the ladder is set-up for use, it must be placed on firm level ground and without any type of slippery condition present at either the base or top support points.
• Only one person at a time is permitted on a ladder unless the ladder is specifically designed for more than one climber (such as a Trestle Ladder).
• Ladders must not be placed in front of closed doors that can open toward the ladder. The door must be blocked open, locked, or guarded.
• Read the safety information labels on the ladder. The on-product safety information is specific to the particular type of ladder on which it appears. The climber is not considered qualified or adequately trained to use the ladder until familiar with this information.
Most ladder accidents occur because of overreaching while standing on ladders, failure to secure ladders, climbing one-handed, standing on the top rung or platform, using worn or damaged ladders, leaving tools on ladders that fall onto someone’s head. Never climb a ladder until you have inspected it. Make sure there are no cracks in the frame, loose or damaged rungs, broken locks or pulleys, or frayed or worn ropes.
Climb safely on a ladder. Climb facing the ladder and using both hands to grab the rungs. Do not wear loose clothing that can become entangled and be conscious of belts, buckles, and holsters which stick out. Do not carry heavy or bulky loads. Do not drape your arms around the rungs if sick dizzy or panicky. When working in a high traffic area place warning signs or barriers to inform passersby of possible danger. Lock doors that could swing open. Ask a coworker to guard the ladder.
The Three Point-of-Contact Climb
Factors contributing to falls from ladders include haste, sudden movement, lack of attention, the condition of the ladder (worn or damaged), the user's age or physical condition, or both, and the user's footwear.
Although the user's weight or size typically does not increase the likelihood of a fall, improper climbing posture creates user clumsiness and may cause falls. Reduce your chances of falling during the climb by:
• Wearing slip-resistant shoes with heavy soles to prevent foot fatigue;
• Cleaning the soles of shoes to maximize traction;
• Using towlines, a tool belt, or an assistant to convey materials so that the climber's hands are free when climbing;
• Climbing slowly and deliberately while avoiding sudden movements;
• Never attempt to move a ladder while standing on it
OSHA Ladder Safety Documents
Agriculture: Protecting Workers from Tripod Orchard Ladder Injuries QuickCard New
(OSHA 3705 - 2014)
Agriculture: Safe Use of Tripod Orchard Ladders Fact Sheet New
(OSHA FS-3728– 2014)
Ladder Safety: Reducing Falls in Construction: Safe Use of Extension Ladders Fact Sheet New
(OSHA FS-3660 - 2013)
Ladder Safety: Reducing Falls in Construction: Safe Use of Job-made Wooden Ladders Fact Sheet New
(OSHA FS-3661 - 2013)
Ladder Safety: Reducing Falls in Construction: Safe Use of Stepladders Fact Sheet New
(OSHA FS-3662 - 2013)

RIGHT
Properly set-up and use the ladder following safety instructions and warnings. Wear shoes with non-slip soles.
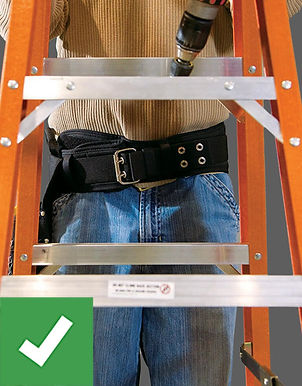
RIGHT
Center body on the ladder and keep belt buckle between the rails while maintaining a firm grip.

RIGHT
Haul materials with a line rather than carry them up an extension ladder. Use extra caution when carrying anything on a ladder.
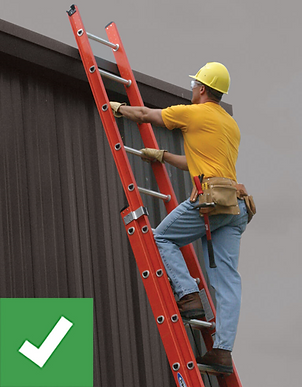
RIGHT
Climb facing the ladder, move one step at a time, and firmly set one foot before moving the other.

RIGHT
Have another person help with a heavy ladder. Have another person hold the ladder while you are working on it.

WRONG
DON'T stand above the second step from the top of a stepladder or the fourth rung from the top of an extension ladder.
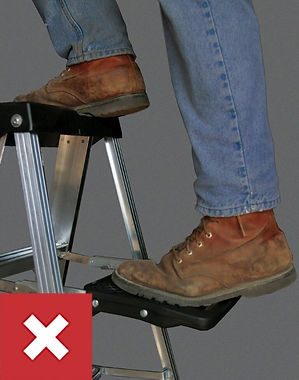
WRONG
DON'T climb on the back of a stepladder. DON'T stand or sit on a stepladder top or pail shelf.

WRONG
DON'T climb a ladder if you are not physically and mentally up to the task.

WRONG
DON'T climb a closed ladder, it may slip out from under you.
Sectional Ladder Set-Up and Safety
Most ladder accidents occur because of overreaching while standing on ladders, failure to secure ladders, climbing one-handed, standing on the top rung or platform, using worn or damaged ladders, leaving tools on ladders that fall onto someone’s head. Never climb a ladder until you have inspected it. Make sure there are no cracks in the frame, loose or damaged rungs, broken locks or pulleys, or frayed or worn ropes.


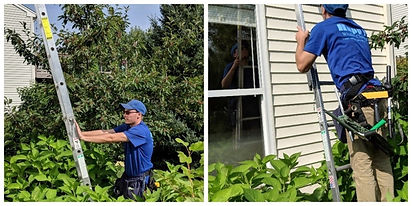
1. When moving or carrying a ladder be aware of your surroundings, if you think at any time you might lose control of the ladder it is good to have an idea of which direction to send it.
2. Make sure to place all pieces evenly across your shoulder and use your legs not your back to lift.
3) When at the setup point place all pieces as close to the side of the house as possible to be able to manage the ladder as much as possible. Never allow the ladder to touch the glass (this will cause you to break a seal and possibly the glass). Watch for overhead wires. Watch for bees’ nest. Make sure the end of the top section is covered with a cotton bonnet to protect any surface it encounters.
4. Always check that the ladder is level, and at the correct angle by bringing your arms straight out at shoulder height. You should be able to place your palms on the ladder sides with your body erect and your feet touching the ladder's feet.
5. When you get on the first step of the ladder get into the habit of jumping on the rung while you’re only a foot off the ground to check if the ladder is going to move. It's best to find out at this point.
Protecting Your Back When Lifting:
Think before you lift. Test the load before lifting it. Place feet shoulder-width apart close to the object, then bend the knees. Get a secure grip on the object. Lift with the legs, keeping the back straight. Lift evenly and slowly, do not jerk the load. Keep the load as close to the body as possible. If you must change the direction that you are facing while carrying a load do not twist the torso, but rather turn the feet in the direction of intended travel. Allow the body to follow the feet. When moving with the load keep it close to the body. Watch for slip and fall hazards. To let the load down, follow the steps in reverse.
Know how to avoid dangerous motions. Don’t overdo it, ask for help. And take care of your back it is the only one you’ve got!
COVID PROTOCOLS
Construction Industry Safety Coalition Recommendations:
COVID-19 Exposure Prevention, Preparedness, and Response Plan for Construction
****
The purpose of this plan is to outline the steps that every employer and employee can take to reduce the risk of exposure to COVID-19. The plan describes how to prevent worker exposure to coronavirus, protective measures to be taken on the Jobsite, personal protective equipment and work practice controls to be used, cleaning and disinfecting procedures, and what to do if a worker becomes sick.
****
Happy Window Cleaning® takes the health and safety of our employees very seriously. With the spread of the coronavirus or “COVID-19,” a respiratory disease caused by the SARS- CoV-2 virus, we all must remain vigilant in mitigating the outbreak. This is particularly true for the construction industry. To be safe and maintain operations, The Construction Industry Safety Coalition developed this COVID-19 Exposure Prevention, Preparedness, and Response Plan. The original document has, with the help of the Michigan Occupational, Health, and Safety Administration, been edited to be Michigan-Specific. This plan will be implemented throughout THE COMPANY and at all of our job sites. CISC has also identified a team of employees to monitor available U.S. Center for Disease Control and Prevention (“CDC”) and the Occupational Safety and Health Administration (“OSHA”) guidance on the virus.
This Plan is based on currently available information from the CDC, OSHA, and MIOSHA and is subject to change based on further information provided by the CDC, OSHA, MIOSHA, and other public officials. While these agencies have been consulted on this document, they have not been asked to endorse it. Happy Window Cleaning® may also amend this Plan based on operational needs.
I. Responsibilities of Managers and Supervisors
All managers and supervisors must be familiar with this Plan and be ready to answer questions from employees. Managers and supervisors must set a good example by following this Plan at all times. This involves practicing good personal hygiene and job site safety practices to prevent the spread of the virus. Managers and supervisors must encourage this same behavior from all employees.
II. Responsibilities of Employees
We are asking every one of our employees to help with our prevention efforts while at work. To minimize the spread of COVID-19 at our job sites, we all must play our part. As set forth below, THE COMPANY has instituted various housekeeping, social distancing, and other best practices at our job sites. All employees must follow these. Also, employees are expected to report to their managers or supervisors if they are experiencing signs or symptoms of COVID-19, as described below. If you have a specific question about this Plan or COVID-19, please ask your manager or supervisor. If they cannot answer the question, please contact [ADD TITLE HERE].
OSHA and the CDC have provided the following control and preventative guidance to all workers, regardless of exposure risk:
• Frequently wash your hands with soap and water for at least 20 seconds. When soap and running water are unavailable, use an alcohol-based hand rub with at least 60% alcohol.
• Avoid touching your eyes, nose, or mouth with unwashed hands.
• Follow appropriate respiratory etiquette, which includes covering for coughs and sneezes.
• Follow social distancing recommendations and stay away six feet or more from other people.
Also, employees must familiarize themselves with the symptoms of COVID-19:
• Coughing;
• Fever;
• Shortness of breath, difficulty breathing; and
• Early symptoms such as chills, body aches, sore throat, headache, diarrhea, nausea/vomiting, and runny nose.
If you develop a fever and symptoms of respiratory illness, such as cough or shortness of breath, DO NOT GO TO WORK and call your healthcare provider right away. Likewise, if you come into close contact with someone showing these symptoms, call your healthcare provider right away.
III. Job Site Protective Measures
THE COMPANY has instituted the following protective measures at all job sites.
A. General Safety Policies and Rules
• Any employee/contractor/visitor showing symptoms of COVID-19 will be asked to leave the job site and return home.
• Safety meetings will be by telephone, if possible. If safety meetings are conducted in-person, attendance will be collected verbally and the foreman/superintendent will sign-in each attendee. Attendance will not be tracked through passed-around sign-in sheets or mobile devices. During any in-person safety meetings, avoid gathering in groups of more than 10 people and participants must remain at least six (6) feet apart.
• Employees must avoid physical contact with others and direct employees/contractors/visitors to increase personal space to at least six (6) feet, where possible. Where work trailers are used, only necessary employees should enter the trailers and all employees should maintain social distancing while inside the trailers.
• All in-person meetings will be limited and participants must remain at least six feet apart. To the extent possible, meetings will be conducted by telephone.
• Employees will be encouraged to stagger breaks and lunches, if practicable, to reduce the size of any group at any one time to less than ten (10) people.
• THE COMPANY understands that due to the nature of our work, access to running water for handwashing may be impracticable. In these situations, THE COMPANY will provide 5- to 10-gallon water jugs and foaming antibacterial soap for handwashing. Where this is infeasible alcohol-based hand sanitizers containing at least 60% alcohol and/or wipes may be used.
• Employees should limit the use of co-workers’ tools and equipment. To the extent tools must be shared, THE COMPANY will provide alcohol-based wipes to clean tools before and after use. When cleaning tools and equipment, consult manufacturing recommendations for proper cleaning techniques and restrictions.
• Employees are encouraged to limit the need for N95 respirator use, by using engineering and work practice controls to minimize dust. Such controls include the use of water delivery and dust collection systems, as well as limiting exposure time.
• THE COMPANY will divide crews/staff into two (2) groups where possible so that projects can continue working effectively if one of the divided teams is required to quarantine.
• As part of the division of crews/staff, THE COMPANY will designate employees into dedicated shifts, at which point, employees will remain with their dedicated shifts for the remainder of the project. If there is a legitimate reason for an employee to change shifts, THE COMPANY will have sole discretion in making that alteration.
• Employees are encouraged to minimize ride-sharing. While in-vehicle, employees must ensure adequate ventilation.
• If practicable, employees should use/drive the same truck or piece of equipment every shift.
• A supply of potable water must be available to all employees in all places of employment. Instead of using a common source of drinking water, such as a cooler, employers may provide individual use water bottles.
[INSERT ADDITIONAL PRECAUTIONS THAT MAY BE SPECIFIC TO YOUR
BUSINESS/OPERATIONS/PROJECTS] Additional Jobsite Safety Precautions Include:
A. Workers entering Occupied Building and Homes
• When employees perform construction and maintenance activities within occupied homes, office buildings, and other establishments, these work locations present unique hazards with regards to COVID-19 exposures. All such workers should evaluate the specific hazards when determining best practices related to COVID- 19.
• During this work, employees must sanitize the work areas upon arrival, throughout the workday, and immediately before departure. THE COMPANY will provide alcohol-based wipes for this purpose.
• Employees should ask other occupants to keep a personal distance of six (6) feet at a minimum. Workers should wash or sanitize hands immediately before starting and after completing the work.
B. Job Site Visitors
• The number of visitors to the job site, including the trailer or office, will be limited to only those necessary for the work.
• All visitors will be screened before being allowed on the job site. If the visitor answers “yes” to any of the following questions, he/she should not be permitted to access the job site:
- Have you been confirmed positive for COVID-19?
- Are you currently experiencing, or recently experienced, any acute respiratory illness symptoms such as fever, cough, or shortness of breath?
- Have you been in close contact with any persons who have been confirmed positive for COVID-19?
- Have you been in close contact with any persons who have traveled and are also exhibiting acute respiratory illness symptoms?
• Site deliveries will be permitted but should be properly coordinated in line with the employer’s minimal contact and cleaning protocols. Delivery personnel should remain in their vehicles if at all possible.
C. Personal Protective Equipment and Work Practice Controls
• In addition to regular PPE for workers engaged in various tasks (fall protection, hard hats, hearing protection), employers will also provide:
Gloves: Gloves should be worn at all times while on-site. The type of glove worn should be appropriate to the task. Cloth gloves shall not be worn when operating rotating equipment such as a drill or a powered threading machine. If gloves are not typically required for the task, then any type of glove is acceptable, including nitrile, latex, or vinyl gloves.
Employees should avoid sharing gloves.
- Eye protection: Eye protection should be worn at all times while on-site.
- NOTE: The CDC is currently not recommending that healthy people wear N95 respirators to prevent the spread of COVID-19. Employees shall wear N95 respirators if required by the work. If N-95 is not available, a higher level of respiratory protection is required.
- In addition to providing PPE, the following Work Practice Controls should also be followed:
- Keep dust down by using engineering and work practice controls, specifically through the use of water delivery and dust collection systems.
- Limit exposure time to the extent practicable.
- Isolate workers in dusty operations by using a containment structure or distance to limit dust exposure to those employees who are conducting the tasks, thereby protecting nonessential workers and bystanders.
• Institute a rigorous housekeeping program to reduce dust levels on the job site.
IV. Job Site Cleaning and Disinfecting
THE COMPANY has instituted regular housekeeping practices, which includes cleaning and disinfecting frequently used tools and equipment, and other elements of the work environment, where possible. Employees should regularly do the same in their assigned work areas. If protective equipment is required and is worn in direct contact with the skin, the equipment shall be sanitized before being reissued to another employee.
• Jobsite trailers and break/lunchroom areas will be cleaned at least once per day. Employees performing cleaning will be issued proper personal protective equipment (“PPE”), such as nitrile, latex, or vinyl gloves and gowns, as recommended by the CDC.
• Any trash collected from the job site must be changed frequently by someone wearing nitrile, latex, or vinyl gloves.
• Any portable job site toilets should be cleaned by the leasing company at least three times per week and disinfected on the inside. THE COMPANY will ensure that hand sanitizer dispensers are always filled. Frequently touched items (i.e. door pulls and toilet seats) will be disinfected after each use.
• Company vehicles and equipment/tools should be cleaned at least once per day and before the change in operator or rider. Gloves and any other disposable PPE used for cleaning and disinfecting the vehicle should be removed and disposed of immediately after cleaning. Hands should be washed or sanitized immediately after removal of gloves and other PPE.
• If an employee has tested positive for COVID-19, OSHA has indicated that there is typically no need to perform special cleaning or decontamination of work environments, unless those environments are visibly contaminated with blood or other bodily fluids. Notwithstanding this, THE COMPANY will clean those areas of the job site, using the CDC guideline found at www.cdc.gov/coronavirus/2019- ncov/disinfecting-building-facility.html, that a confirmed-positive individual may have come into contact with before employees can access that workspace again.
• THE COMPANY will ensure that any disinfection shall be conducted using one of the following:
- Common EPA-registered household disinfectant;
- Alcohol solution with at least 70% alcohol; or
- Diluted household bleach solutions (these can be used if appropriate for the surface).
• THE COMPANY will maintain Safety Data Sheets of all disinfectants used on-site and will train all cleaning staff on-site before assigning cleaning tasks.
[INSERT ADDITIONAL CLEANING REQUIREMENTS IF YOU USE HAZARDOUS
CHEMICALS ON SITE] Additional Cleaning and Disinfection Guidelines Include:
V. Jobsite Exposure Situations
• Employee Exhibiting COVID-19 Symptoms
If an employee exhibits COVID-19 symptoms, the employee must remain at home until he or she is symptom-free for 72 hours (3 full days) without the use of fever-reducing or other symptom-altering medicines (e.g., cough suppressants). THE COMPANY will similarly require an employee that reports working with symptoms to return home until they are symptom-free for 72 hours (3 full days). To the extent practical, employees are required to obtain a doctor’s note clearing them to return to work.
• Employee Tests Positive for COVID-19
An employee that tests positive for COVID-19 will be directed to self-quarantine away from work. Employees that test positive and are symptom-free may return to work when at least seven (7) days have passed since the date of their first positive test, and have not had a subsequent illness. Employees that test positive and are directed to care for themselves at home may return to work when: (1) at least 72 hours (3 full days) have passed since recovery; and (2) at least seven (7) days have passed since symptoms first appeared. Employees that test positive and have been hospitalized may return to work when directed to do so by their medical care provider. THE COMPANY will require an employee to provide documentation clearing their return to work.
• Employee Has Close Contact with a Tested Positive COVID-19 Individual
Employees that have come into close contact with a confirmed-positive COVID-19 individual (co-worker or otherwise), will be directed to self-quarantine for 14 days from the last date of close contact with the carrier. Close contact is defined as six (6) feet for a prolonged period.
If THE COMPANY learns that an employee has tested positive, THE COMPANY will investigate co-workers that may have had close contact with the confirmed- positive employee in the prior 14 days and direct those individuals that have had close contact with the confirmed-positive employee to self-quarantine for 14 days from the last date of close contact with the carrier. If an employee learns that he or she has come into close contact with a confirmed-positive individual outside of the workplace, he/she must alert a manager or supervisor of the close contact and also self-quarantine for 14 days from the last date of close contact with the carrier.
VI. OSHA Recordkeeping
THE COMPANY will adhere to the guidelines set by federal OSHA regarding COVID-19 and Injury & Illness recordkeeping.
Until further notice, however, THE COMPANY will not make work-relatedness determinations, except where:
(1) There is objective evidence that a COVID-19 case may be work-related. This could include, for example, some cases developing among workers who work closely together without an alternative explanation; and
(2) The evidence was reasonably available to THE COMPANY. Examples of reasonably available evidence include information given to THE COMPANY by employees, as well as information that THE COMPANY learns regarding its employees’ health and safety in the ordinary course of managing its business and employees.
When recorded, COVID-19 should be coded as a respiratory illness on Form 300. Because this is an illness, if an employee voluntarily requests that his or her name not be entered on the log, THE COMPANY will comply.
If an employee has a confirmed case of COVID-19, THE COMPANY will conduct an assessment of any workplace exposures to determine if the case is work-related. Work-relatedness is presumed for illnesses that result from events or exposures in the work environment unless it meets certain exceptions. One of those exceptions is that the illness involves signs or symptoms that surface at work but result solely from a non-work-related event or exposure that occurs outside of the work environment. Thus, if an employee develops COVID-19 solely from exposure outside of the work environment, it would not be work-related, and thus not recordable.
THE COMPANY’s assessment will consider the work environment itself, the type of work performed, the risk of person-to-person transmission given the work environment, and other factors such as community spread. Further, if an employee has a confirmed case of COVID- 19 that is considered work-related, THE COMPANY will report the case to OSHA if it results in a fatality within 30 days or an in-patient hospitalization within 24-hours of the exposure incident occurring.
VII. Confidentiality/Privacy
Except for circumstances in which THE COMPANY is legally required to report workplace occurrences of communicable disease, the confidentiality of all medical conditions will be maintained following applicable law and to the extent practical under the circumstances. When it is required, the number of persons who will be informed of an employee’s condition will be kept at the minimum needed not only to comply with legally- required reporting but also to assure proper care of the employee and to detect situations where the potential for transmission may increase. A sample notice to employees is attached to this Plan. THE COMPANY reserves the right to inform other employees that a co-worker (without disclosing the person’s name) has been diagnosed with COVID-19 if the other employees might have been exposed to the disease so the employees may take measures to protect their health.
VIII. General Questions
Given the fast-developing nature of the COVID-19 outbreak, THE COMPANY may modify this Plan on a case by case basis. If you have any questions concerning this Plan, please contact [ADD TITLE HERE.]
Essential Industry Employee
Re: Shelter-in-Place Orders
To whom it may concern:
Please be informed that the bearer of this letter is employed at Happy Window Cleaning®, located at [COMPANY ADDRESS]. THE COMPANY is a [name type of contractor]. We have reviewed all applicable Orders and have determined that our operations qualify as essential/critical infrastructure and that we can continue to operate under those Orders.
Employees in possession of this letter have been deemed essential to the minimum basic operations of our business. All non-essential personnel has been notified to work remotely until further notice. Employees who are critical to the minimum basic operations of the business have been instructed to comply with social distancing rules/requirements in the jurisdiction, as well as other safety and health precautions.
If you have questions regarding the nature or scope of this letter, please do not hesitate to contact [insert contact name] at [insert contact number and/or email].
Sincerely,
EXECUTIVE NAME
TITLE
Employee Notification
DATE: [DATE]
TO: [CLOSE CONTACT EMPLOYEE]
FROM: [COMPANY REP]
We have been informed by one of our [employees/customer/vendor/etc] working at [SITE] that he/she has a confirmed case of COVID-19, commonly known as “Coronavirus,” based on test results obtained on [DATE]. Per company policy, this [employee/customer/vendor/etc] has been directed to self-quarantine until permitted to return to work.
We are alerting you to this development because, based on THE COMPANY’s investigation, we believe that you may have come into contact with the confirmed-positive case, on or about [DATE]. Based on Company policy we are directing you not to report to work (i.e., self-quarantine) until, at least, [14 days from the last contact with the confirmed case]. In the interim, we encourage you to seek medical advice and a COVID-19 test, especially if you are exhibiting symptoms of the virus.
If you do not test positive for COVID-19, or experience symptoms, by [14 days from the last contact with the confirmed case], you may return to work. However, please inform [COMPANY CONTACT] if any of the following occur during your self-quarantine: you experience flu-like symptoms, including fever, cough, sneezing, or sore throat; or you test positive for COVID-19.
We are committed to providing a safe environment for all of our employees and top-quality service to our customers. It is in the interest of those goals that we provide this information out of an abundance of caution.
We also want to take this opportunity to remind you that one of our core values as a company is respect for and among our employees [or customers]. We will treat information regarding the identity of employees [or customers] with suspected or confirmed cases of COVID-19 as confidential to the extent practicable and will comply with applicable laws regarding the handling of such information. Further, per Company policy, we will not tolerate harassment of, or discrimination or retaliation against, employees [or anyone].
Please contact [COMPANY CONTACT AWARE OF APPROPRIATE PROTOCOLS] at
[PHONE NUMBER] if you have any questions or concerns.
For more information about COVID-19, please visit the Michigan COVID-19 website at https://www.michigan.gov/coronavirus
COVID-19 Checklist for Employers and Employees
Know the Symptoms of COVID-19
• Coughing, fever, shortness of breath, and difficulty breathing.
• Early symptoms may include chills, body aches, sore throat, headache, diarrhea, nausea/vomiting, and runny nose. If you develop a fever and symptoms of respiratory illness, DO NOT GO TO WORK and call your health-care provider immediately. Do the same thing if you come into close contact with someone showing these symptoms.
Employer Responsibilities
• Develop a COVID-19 Exposure Action Plan.
• Conduct safety meetings (toolbox talks) by phone if possible. If not, instruct employees to maintain 6-feet between each other. The foreman/supervisor will track attendance verbally rather than having employees sign an attendance sheet.
• Access to the job site and work trailer will be limited to only those necessary for the work.
• All visitors will be pre-screened to ensure they are not exhibiting symptoms.
• Employees, contractors, and visitors will be asked to leave the job site and return home if they are showing symptoms.
• Provide hand sanitizer and maintain Safety Data Sheets of all disinfectants used on site.
• Provide protective equipment (PPE) to any employees assigned cleaning/disinfecting tasks.
• Talk with business partners about your response plans. Share best practices with other businesses in your communities (especially those in your supply chain), chambers of commerce, and associations to improve community response efforts.
Employee Responsibilities
• Become familiar with the Exposure Action Plan and follow all elements of the Plan.
• Practice good hygiene: wash hands with soap and water for at least 20 seconds. If these are not available, use an alcohol-based hand rub with at least 60% alcohol. Avoid touching your face, eyes, food, etc. with unwashed hands.
Cleaning/Disinfecting Job Sites and Other Protective Measures
• Clean and disinfect frequently used tools and equipment regularly. This includes other elements of the job site where possible. Employees should regularly do the same in their assigned work areas.
• Clean shared spaces such as trailers and break/lunchrooms at least once per day.
• Disinfect shared surfaces (door handles, machinery controls, etc.) regularly.
• Avoid sharing tools with co-workers. If not, disinfect before and after each use.
• Arrange for any portable job site toilets to be cleaned by the leasing company at least twice per week and disinfected on the inside.
• Trash collected from the job site must be changed frequently by someone wearing gloves.
Personal Protective Equipment and Alternate Work Practice Controls
• Provide and wear the proper PPE.
• Keep the dust down by using engineering and work practice controls, specifically through the use of water delivery and dust collection systems.
COVID-19 Toolbox Talk
What is COVID-19?
The novel coronavirus, COVID-19 is one of seven types of known human coronaviruses. COVID-19, like the MERS and SARS coronaviruses, likely evolved from a virus previously found in animals. The remaining known coronaviruses cause a significant percentage of colds in adults and children, and these are not a serious threat for otherwise healthy adults.
Patients with confirmed COVID-19 infection have reportedly had mild to severe respiratory illness with symptoms such as fever, cough, and shortness of breath.
According to the U.S. Department of Health and Human Services/Centers for Disease Control and Prevention (“CDC”), Chinese authorities identified an outbreak caused by a novel—or new—coronavirus. The virus can cause mild to severe respiratory illness. The outbreak began in Wuhan, Hubei Province, China, and has spread to a growing number of other countries— including the United States.
How is COVID-19 Spread?
COVID-19, like other viruses, can spread between people. Infected people can spread COVID-19 through their respiratory secretions, especially when they cough or sneeze. According to the CDC, spread from person-to-person is most likely among close contacts (about 6 feet). Person-to-person spread is thought to occur mainly via respiratory droplets produced when an infected person coughs or sneezes, like how influenza and other respiratory pathogens spread. These droplets can land in the mouths or noses of people who are nearby or possibly be inhaled into the lungs. It is currently unclear if a person can get COVID-19 by touching a surface or object that has the virus on it and then touching their mouth, nose, or possibly their eyes.
In assessing potential hazards, employers should consider whether their workers may encounter someone infected with COVID-19 in the course of their duties. Employers should also determine if workers could be exposed to environments (e.g., worksites) or materials (e.g., laboratory samples, waste) contaminated with the virus.
Depending on the work setting, employers may also rely on the identification of sick individuals who have signs, symptoms, and/or a history of travel to COVID-19-affected areas that indicate potential infection with the virus, to help identify exposure risks for workers and implement appropriate control measures.
There is much more to learn about the transmissibility, severity, and other features associated with COVID-19, and investigations are ongoing.
COVID-19 Prevention and Work Practice Controls:
Worker Responsibilities
• Frequently wash your hands with soap and water for at least 20 seconds. When soap and running water are unavailable, use an alcohol-based hand rub with at least 60% alcohol. Always wash hands that are visibly soiled.
• Cover your mouth and nose with a tissue when you cough or sneeze or use the inside of your elbow.
• Avoid touching your eyes, nose, or mouth with unwashed hands.
• Avoid close contact with people who are sick.
• Employees who have symptoms (i.e., fever, cough, or shortness of breath) should notify their supervisor and stay home—DO NOT GO TO WORK.
• Sick employees should follow the CDC-recommended steps. Employees should not return to work until the criteria to discontinue home isolation are met, in consultation with healthcare providers and state and local health departments.
General Job Site / Office Practices
• Clean AND disinfect frequently touched objects and surfaces such as workstations, keyboards, telephones, handrails, and doorknobs. Dirty surfaces can be cleaned with soap and water before disinfection. To disinfect, use products that meet EPA’s criteria for use against the SARS-CoV-2external icon, the cause of COVID-19, and are appropriate for the surface.
• Avoid using other employees’ phones, desks, offices, or other work tools and equipment, when possible. If necessary, clean and disinfect them before and after use.
• Clean and disinfect frequently used tools and equipment regularly.
- This includes other elements of the job site where possible.
- Employees should regularly do the same in their assigned work areas.
• Clean shared spaces such as trailers and break/lunchrooms at least once per day.
• Disinfect shared surfaces (door handles, machinery controls, etc.) regularly.
• Avoid sharing tools with co-workers if it can be avoided. If not, disinfect before and after each use.
• Arrange for any portable job site toilets to be cleaned by the leasing company at least twice per week and disinfected on the inside.
• Any trash collected from the job site must be changed frequently by someone wearing gloves.
• In addition to regular PPE for workers engaged in various tasks (fall protection, hard hats, hearing protection), employers will also provide:
- Gloves: Gloves should be worn at all times while on-site. The type of glove worn should be appropriate to the task. If gloves are not typically required for the task, then any type of glove is acceptable, including latex gloves. Gloves should not be shared if at all possible.
- Eye protection: Eye protection should be worn at all times while on-site.
EMERGENCY PROCEDURES
Emergencies can be a fact of life. But being prepared can make the difference between a measured response and a full-blown crisis.
Keep emergency contact information sheets on every employee of your franchise and make sure that they are up to date.
Should an emergency arise that goes beyond the scope of your franchise, please contact Happy Window Cleaning® HQ as soon as possible for advice and direction. All departments are skilled in handling different types of emergencies and we remain vigilant about these possibilities at all times.
• Preventing Accidents and Injuries
• Crisis Management Policy
• Reporting Accidents
• Worker’s Compensation Issues
• Fire Safety
• Robbery / Burglary
• Unruly Customers
• Using the Alarm System
SAFETY DISCIPLINE
All employees, including all levels of management, are held accountable for obeying site safety and health rules. The following four-step disciplinary policy may be applied to everyone by the appropriate level of Supervisor:
The basic objective of the safety program is to prevent accidents and injuries and to reduce operating costs by following safe practices. The use of safe practices prevents lost time, equipment, and property damage, and reduces expenditures of funds for medical care, compensation, and liability. It is recognized that to accomplish these tasks, a sound safety program focusing on accident prevention must be integrated into the day-to-day activities of each employee. All employees must think, talk, and work safely.
A certain number of safety-related rules and policies are necessary at work. Common sense tells most of us what should and should not be done, but in other instances, safety rules, policies, and procedures are established by the Company to govern conduct while at work, and to promote a safe work environment for all employees.
Any employee who commits an act that is offensive to the rules of common sense, or an act that violates accepted safety rules/policies/procedures, will be disciplined, up to and including termination of employment. The nature of the discipline will depend upon the nature of the violation and the surrounding circumstances.
If disciplinary action is taken against the employee, the employee may appeal it if the employee feels the disciplinary action was wrong. The employee may present a written appeal to the employee’s Supervisor. The employee’s appeal will be given careful consideration.
The following list of reasons for safety-related discipline is not intended to be all-inclusive; the mere fact that a possible violation is not listed does not mean that it would not result in disciplinary action. Common sense tells most of us what would constitute a violation in most circumstances.
VIOLATIONS THAT WILL RESULT IN DISCIPLINARY ACTION BEING ISSUED
⦁ Horseplay, such as running, shoving, pushing, throwing objects, and/or any type of horseplay which could jeopardize the employee’s safety or the safety of others.
⦁ Failure to immediately report injuries or refusing to give information to any member of management and/or the Human Resources Administrator.
⦁ Failure to report observed unsafe behavior or conditions.
⦁ Violation of any Company accepted safety procedure, policy, program, or rule.
⦁ Causing unsafe conditions or carelessness regarding safety to self or others, or failure to properly use safety devices or tampering with safety equipment.
⦁ Intentional misuse of or damage to equipment, vehicles, or property of others.
The aforementioned list constitutes some, but not necessarily all, of the kinds of conduct that will result in disciplinary action, up to and including termination of employment.
VIOLATION OF ACCEPTED SAFETY RULES, POLICIES, AND PROCEDURES
Any employee who violates any accepted safety rule, policy, or procedure, whether written or unwritten, shall be subject to this disciplinary action program which may, but need not, include oral warning, written warnings, suspension without pay, or any other discipline, up to and including termination of employment. The Disciplinary Action Schedule contained in this program can be altered, depending on the seriousness of the violation, at management’s discretion.